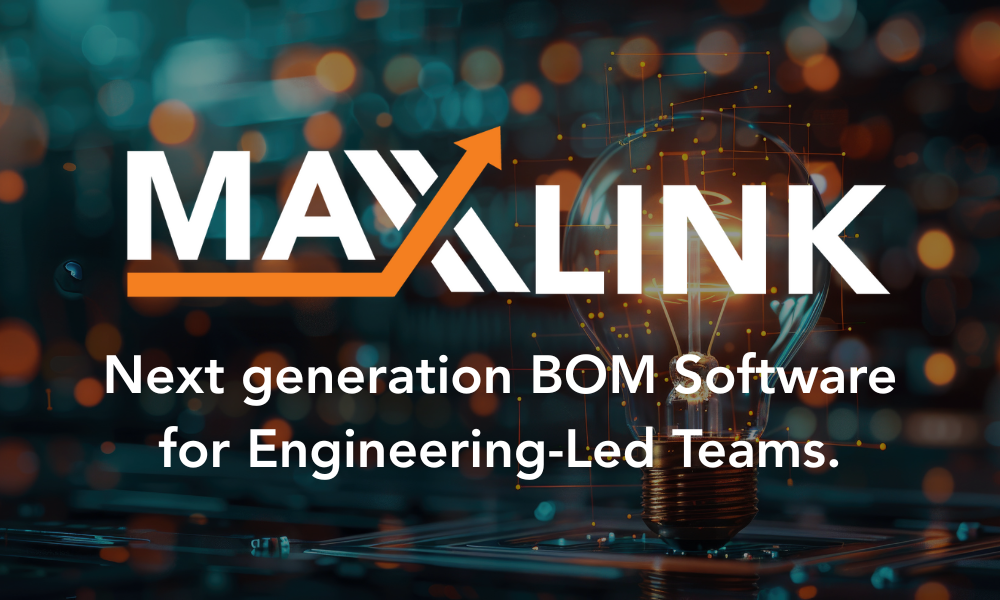
Introducing MaXXlink: A Smarter, Faster Way to Manage Your Bill of Materials
MaXXlink is the next-gen Bill of Materials software for engineering-led teams. Streamline BOM management, boost productivity, and integrate with CAD and ERP systems in minutes. Start your 30-day free trial today.
Read more